1.项目概况
四川省某水泥有限公司现有一条设计日产2500t水泥熟料的预分解窑生产线,由中技国际工程设计,年平均产量2900t/d,烧成热耗为115kg标准煤/t-cl。
预分解系统采用RSP分解炉+五级旋风预热系统,窑采用Ø4×60m斜度3.5的三档窑。
由于原预分解系统存在一定的局限,造成单位能耗高,熟料生产成本高,已经不适应现在的激烈的市场竞争。该水泥有限公司根据企业自身的经营状况以及市场情况,决定对2500t/d水泥熟料生产线进行提产节能技改。该公司2018年9月至10月期间最终做出审慎的决定:使用我派飞特机械有限公司的方案对2500t/d水泥熟料生产线进行提产节能技改。
经过2个月的准备期,和35天的施工期,我公司圆满完成了该公司2500t/d水泥熟料生产线提产节能技改项目。生产线于2018年10月8日投料,10月15日即达产,达到3173t/d,11月16日产量达3213t/d,12月11日产量达3434.19t/d,目前生产稳定。
2.改造前生产线运行瓶颈和主要问题
该水泥有限公司2500t/d生产线建成于2010年,改造前主要存在以下问题:
2.1系统产量不高且不稳定
改造前,系统产量为2900~3000 t/d,由于设计缺陷,系统频繁塌料产量低,熟料强度低,仅55Mpa。
2.2煤耗偏高
生产线标煤耗偏高,基本在114~116kg标煤/t,导致生产成本明显偏高。
2.3氨水消耗量
2016~2017年熟料吨熟料氨水消耗量3kg(排放260mg/m3)
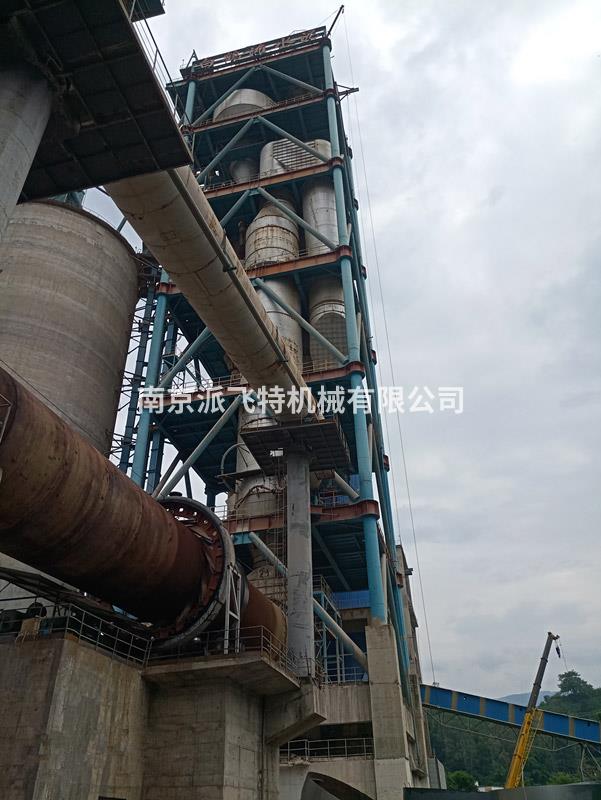
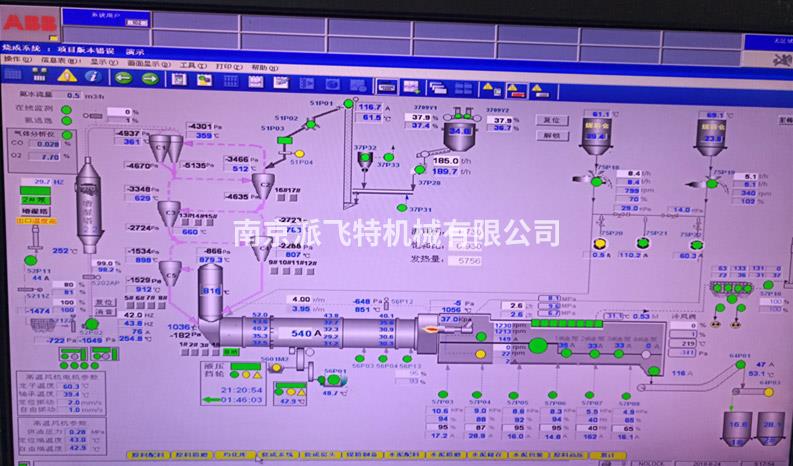
改造前
3.技改内容
3.1技改后指标(合同约定):
熟料产量≥3100t/d
熟料烧成综合标煤耗≤110kg/t-cl
吨熟料氨水消耗量排放200mg/m3时候小于3kg。
3.2改造内容
A.预分解系统主要技改内容:为了提产且节约投资,保留原分解炉并适当加长,增加鹅颈管;为减小系统阻力,加大关键部位的通风面积;调整烟室缩口,使二次风与三次风相匹配。
技改后分解炉系统具有结构简单、阻力系数低、双喷腾效应、湍流回流作用强、物料分散及换热效果好、温度场和浓度场均匀、气固停留时间长、原燃料适应性强等优点。
B.三次风管局部改造:将三次风管改为从分解炉直段切向进入,适当提高三次风进入分解炉的位置,形成还原区。更换新的分解炉燃烧器降低NOX排放。
C.更换全新的烟室,以满足更高的生产需要。
4.改造效果
4.1水泥熟料产量由2900t/d提高到3200t/d以上
10月6日投产后,10月的平均产量为3173t/d,11月的平均产量为3213 t/d。12月11日的日均产量达到了3434 t/d,提升机电流由原来120A上升到130A。
4.2水泥熟料热耗由116 kg标煤/t-cl降至110kg标煤/t-cl以下
根据盘库熟料产量和煤粉称下料量统计值,计算得出系统热耗为107.8~110.5kg标准煤/t-cl。
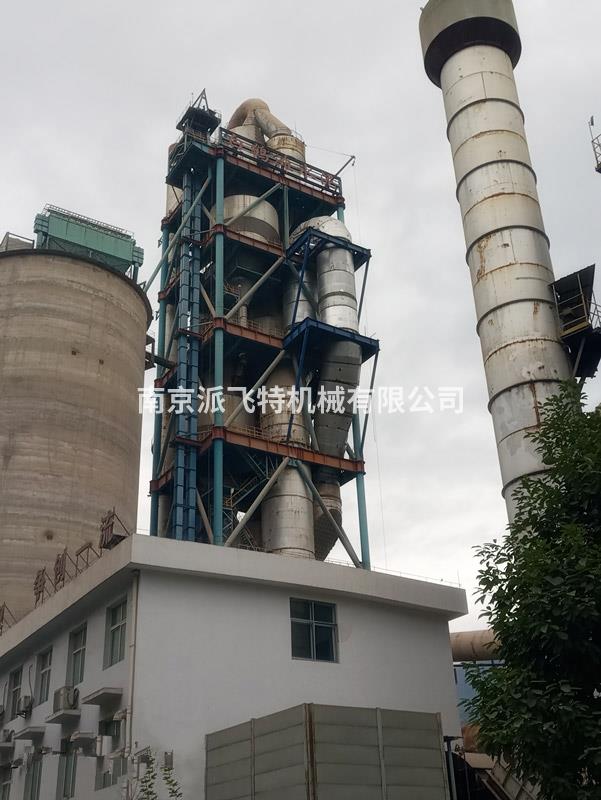
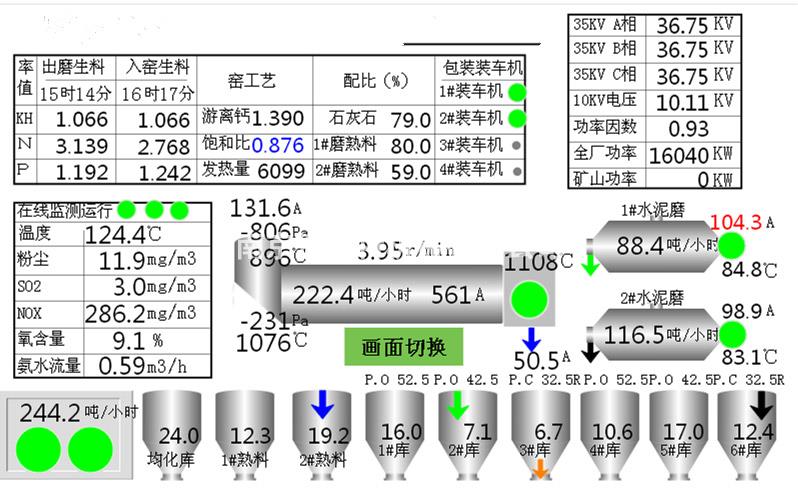
改造后
技改前后主要技术指标对比
5.改造效果和经济效益分析
5.1产能提升
由2900t/d提升至3300t/d,产能提升400t/d,以年运转200天计算,年增加产能10万吨熟料。改造前熟料的平均净利润约100元/吨(不含税),年增利润1000万元。
5.2热耗降低
热耗由原来115kg标煤/t-cl降至109.5标煤/t-cl(煤热值以6000kcal/kg计),年节省用煤量3850吨(年熟料产量70万吨计算),按目前原煤采购价800元/吨计算,年节省费用308万元。
5.3氨水消耗降低
改造后,氨水理论消耗量下降30\%,以年70万吨熟料计算,可节约费用63万元。
5.4熟料强度提升和电耗降低
熟料强度小幅提升,系统电耗小幅降低,由于没有准确数据,暂不进行统计。
综上:技改完成后,年增加经济效益1371万元,本次项目改造总投资499万元,不含建设期的投资回收期为4.3个月。
总结:
此次技改是在原Ø4×60m回转窑不动的情况下,充分考虑了现有原料磨、煤磨、废气处理系统以及窑尾预热器框架和预分解系统等的现状和特点,在进行了原料平衡和热工计算后对系统进行优化,充分发掘现有系统的潜力,并通过改造预分解系统等措施,最终实现Ø4×60m回转窑的提产节能改造的合同目标。
本次烧成系统技术改造投资约499万,停窑实际工期35天。改造后系统产量提高,能耗下降,窑能够保持稳定高产运行,达到了提产节能降耗的改造目的。
在国家加快建设生态文明、大力推进节能减排的政策形势下,本改造项目迎势而上,企业获得了良好经济效益和社会效益,市场竞争能力增强,投资效益显著,得到了业主的信赖。
1.项目概况
四川省某水泥有限公司现有一条设计日产2500t水泥熟料的预分解窑生产线,由中技国际工程设计,年平均产量2900t/d,烧成热耗为115kg标准煤/t-cl。
预分解系统采用RSP分解炉+五级旋风预热系统,窑采用Ø4×60m斜度3.5的三档窑。
由于原预分解系统存在一定的局限,造成单位能耗高,熟料生产成本高,已经不适应现在的激烈的市场竞争。该水泥有限公司根据企业自身的经营状况以及市场情况,决定对2500t/d水泥熟料生产线进行提产节能技改。该公司2018年9月至10月期间最终做出审慎的决定:使用我派飞特机械有限公司的方案对2500t/d水泥熟料生产线进行提产节能技改。
经过2个月的准备期,和35天的施工期,我公司圆满完成了该公司2500t/d水泥熟料生产线提产节能技改项目。生产线于2018年10月8日投料,10月15日即达产,达到3173t/d,11月16日产量达3213t/d,12月11日产量达3434.19t/d,目前生产稳定。
2.改造前生产线运行瓶颈和主要问题
该水泥有限公司2500t/d生产线建成于2010年,改造前主要存在以下问题:
2.1系统产量不高且不稳定
改造前,系统产量为2900~3000 t/d,由于设计缺陷,系统频繁塌料产量低,熟料强度低,仅55Mpa。
2.2煤耗偏高
生产线标煤耗偏高,基本在114~116kg标煤/t,导致生产成本明显偏高。
2.3氨水消耗量
2016~2017年熟料吨熟料氨水消耗量3kg(排放260mg/m3)
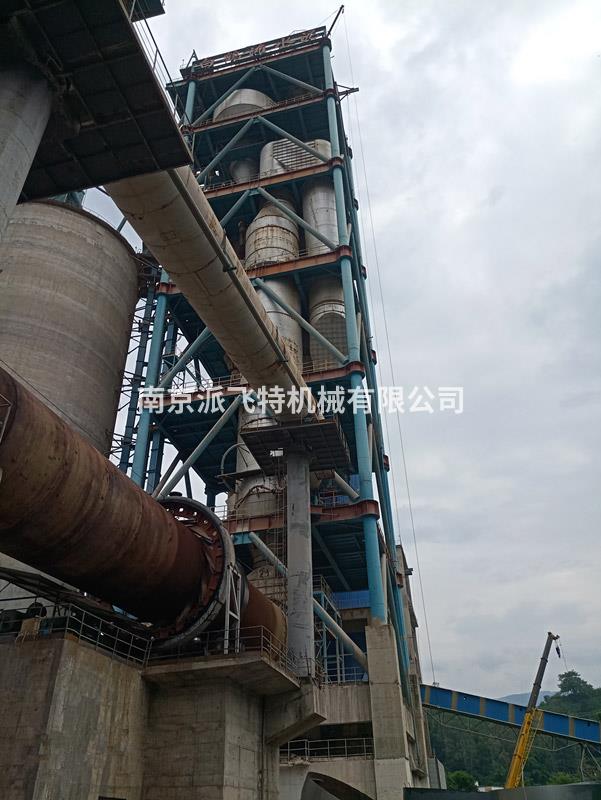
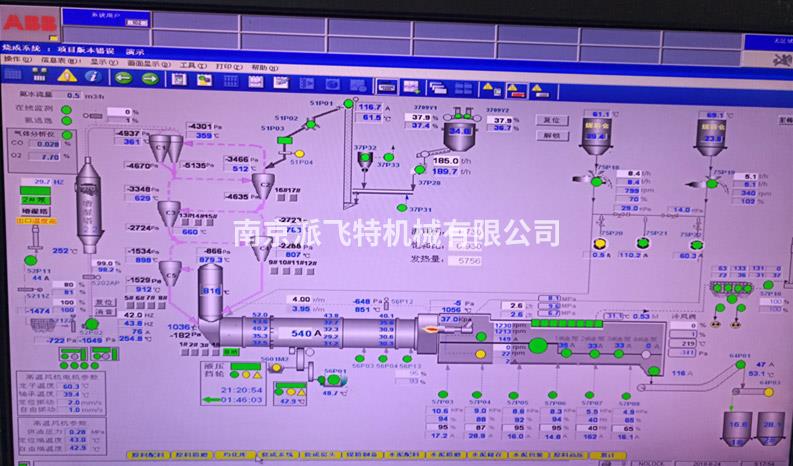
改造前
3.技改内容
3.1技改后指标(合同约定):
熟料产量≥3100t/d
熟料烧成综合标煤耗≤110kg/t-cl
吨熟料氨水消耗量排放200mg/m3时候小于3kg。
3.2改造内容
A.预分解系统主要技改内容:为了提产且节约投资,保留原分解炉并适当加长,增加鹅颈管;为减小系统阻力,加大关键部位的通风面积;调整烟室缩口,使二次风与三次风相匹配。
技改后分解炉系统具有结构简单、阻力系数低、双喷腾效应、湍流回流作用强、物料分散及换热效果好、温度场和浓度场均匀、气固停留时间长、原燃料适应性强等优点。
B.三次风管局部改造:将三次风管改为从分解炉直段切向进入,适当提高三次风进入分解炉的位置,形成还原区。更换新的分解炉燃烧器降低NOX排放。
C.更换全新的烟室,以满足更高的生产需要。
4.改造效果
4.1水泥熟料产量由2900t/d提高到3200t/d以上
10月6日投产后,10月的平均产量为3173t/d,11月的平均产量为3213 t/d。12月11日的日均产量达到了3434 t/d,提升机电流由原来120A上升到130A。
4.2水泥熟料热耗由116 kg标煤/t-cl降至110kg标煤/t-cl以下
根据盘库熟料产量和煤粉称下料量统计值,计算得出系统热耗为107.8~110.5kg标准煤/t-cl。
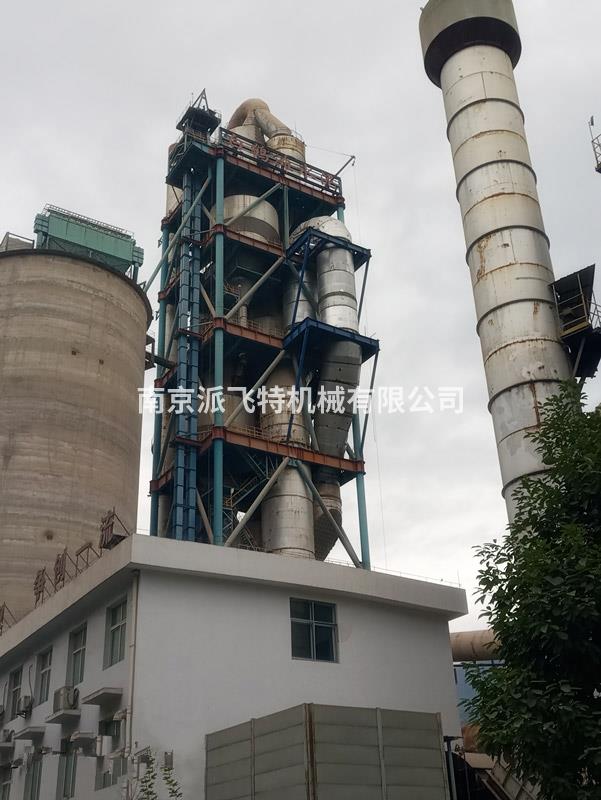
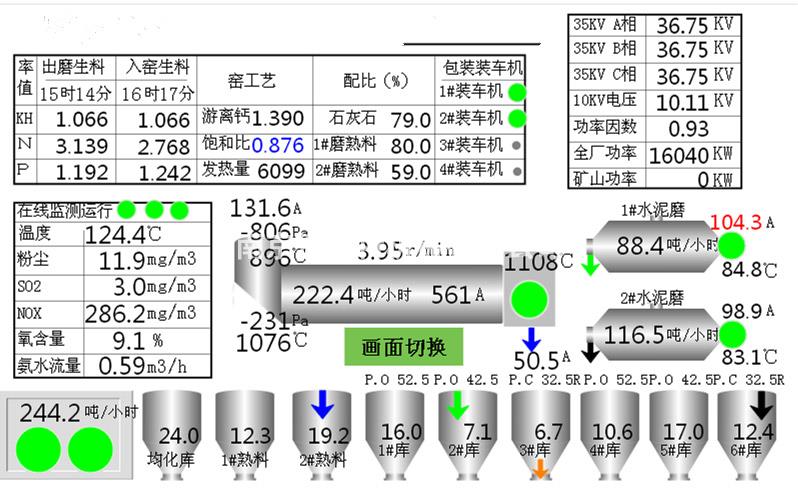
改造后
技改前后主要技术指标对比
5.改造效果和经济效益分析
5.1产能提升
由2900t/d提升至3300t/d,产能提升400t/d,以年运转200天计算,年增加产能10万吨熟料。改造前熟料的平均净利润约100元/吨(不含税),年增利润1000万元。
5.2热耗降低
热耗由原来115kg标煤/t-cl降至109.5标煤/t-cl(煤热值以6000kcal/kg计),年节省用煤量3850吨(年熟料产量70万吨计算),按目前原煤采购价800元/吨计算,年节省费用308万元。
5.3氨水消耗降低
改造后,氨水理论消耗量下降30\%,以年70万吨熟料计算,可节约费用63万元。
5.4熟料强度提升和电耗降低
熟料强度小幅提升,系统电耗小幅降低,由于没有准确数据,暂不进行统计。
综上:技改完成后,年增加经济效益1371万元,本次项目改造总投资499万元,不含建设期的投资回收期为4.3个月。
总结:
此次技改是在原Ø4×60m回转窑不动的情况下,充分考虑了现有原料磨、煤磨、废气处理系统以及窑尾预热器框架和预分解系统等的现状和特点,在进行了原料平衡和热工计算后对系统进行优化,充分发掘现有系统的潜力,并通过改造预分解系统等措施,最终实现Ø4×60m回转窑的提产节能改造的合同目标。
本次烧成系统技术改造投资约499万,停窑实际工期35天。改造后系统产量提高,能耗下降,窑能够保持稳定高产运行,达到了提产节能降耗的改造目的。
在国家加快建设生态文明、大力推进节能减排的政策形势下,本改造项目迎势而上,企业获得了良好经济效益和社会效益,市场竞争能力增强,投资效益显著,得到了业主的信赖。