Technical Service Report for ATOX50 Mill at a Specific Cement Plant's Line Three
Publishdate:2024-08-22 Views:1682
摘要:客户ATOX50原料磨利用检修时间更换磨辊轴承,我公司技术到现场对安装更换过程进行了协助、指导和监督。
Summary: The customer's ATOX50 raw mill utilized the maintenance period to replace the roller bearings. Our company's technician assisted, guided, and supervised the installation and replacement process on-site.
一、至现场时,设备的安装状况 Equipment Installation Status On Site
1、至现场时,磨辊已经解体并部分进行清洗,2#磨辊外间隔套未进行拆卸,位置确认未发生移动。
Upon arrival at the site, the roller had been disassembled and partially cleaned, with the outer distance ring of roller #2 not yet disassembled, and its position confirmed to have not shifted.
2、2#磨辊使用全新的FAG轴承。轴承型号为F-679545.NU(NU20/800-E-M1A)和F-679568.PRL(241/710-B-K30-MB-H44-SA)
Roller #2 used brand new FAG bearings. The bearing models were F-679545. NU (NU20/800-E-M1A) and F-679568. PRL (241/710-B-K30-MB-H44-SA).
3#磨辊使用一只标志仅有“GERMANY X.D”双列圆锥轴承,该轴承为已使用过的旧轴承,轴承滚珠表面镀层有明显的磨损和锈蚀的痕迹,另一只轴承型号为F-679545.NU,全新,生产商为FAG.
Roller #3 used a double-row tapered roller bearing marked only with "GERMANY X.D", which was a used bearing. The coating on the bearing balls showed noticeable wear and rust, and the other bearing model was F-679545.NU, which was new and manufactured by FAG.
二、安装服务过程 Installation Service Process
1、对部件润滑油路进行清理和检查。Cleaning and inspection of the component lubrication oil circuit.
(1)清洗前检查 Inspection before cleaning.
(2)清洗 Cleaning
(3)清洗后 After cleaning
2、主轴和轮毂清理 Cleaning of the main shaft and hub
3、内侧端盖清理、间隔圈清理、骨架油封安装、内侧空气密封内环安装。
Cleaning of the inner cover, distance ring, installation of the rotary shaft seal, the inner sealing ring.
4、用油煮NU20/800轴承内圈并安装到主轴上,安装轴承内间隔套于主轴上。过程中使用铜棒辅助安装。
Heating the inner ring of the NU20/800 bearing in oil and installing it onto the main shaft, then installing the bearing inner distance ring onto the main shaft. A copper rod was used to assist with the installation.
5、安装内侧端盖O型圈,涂抹美孚1500润滑脂于骨架油封唇口,将内侧端盖安装于主轴上并固定。
Installing the inner cover O-ring, applying Mobil 1500 lubricating grease to the lip of the rotary shaft seal, installing and securing the inner cover onto the main shaft.
6、用液氮冷冻安装3#辊外间隔套、2#3#辊NU20/800外圈和241/710轴承。检查间隔套和轴承接触正常。
Using liquid nitrogen to freeze and install the outer distance ring of roller #3, the outer rings of NU20/800 for rollers #2 and #3, and the 241/710 bearing. Ensuring the proper contact between the outer distance ring and the bearing.
7、清理安装轴承外圈和主轴,将主轴小心套入轮毂,用葫芦拉紧,促使241/710轴承内圈与内间隔套紧密接触。用支架撑起主轴,保持轮毂能盘动。
Cleaning the installation of the bearing outer ring and main shaft, carefully placing the main shaft into the hub, and using a hoist to tighten it, ensuring tight contact between the inner ring of the 241/710 bearing and the inner distance ring. Support the main shaft with a stand to keep the hub rotating.
8、清理退卸套,将退卸套安装入磨辊,安装压盘,涂抹密封胶,紧固内侧端盖,转动磨辊,现场采用人工方式逐步紧固压盘螺栓调整241/710轴承游隙,调整结果:2#辊轴承游隙为0.11mm,3#轴承游隙为0.13mm。测量轴承内圈到退卸套端面的高度为:2#平均71.24mm 、3#平均60.50mm,加工压环后,对压环按扭矩对压环螺栓进行了紧固,压环与轴承内圈接触紧密。
Cleaning the conical sleeve, installing it into the roller, installing the bearing retainer ring, applying sealant, tightening the inner cover, and rotating the roller. The bolts of the bearing retainer ring were gradually tightening manually on-site, adjusting the clearance of the 241/710 bearing. The results were that the clearance of the roller #2 bearing was 0.11mm, and the bearing #3 clearance was 0.13mm. The measured height from the bearing inner ring to the end face of the conical sleeve was an average of 71.24mm for #2 and 60.50mm for #3. After processing the bearing retainer ring, the bolts of the bearing retainer ring were tightened according to the torque, ensuring close contact between the bearing retainer ring and the bearing inner ring.
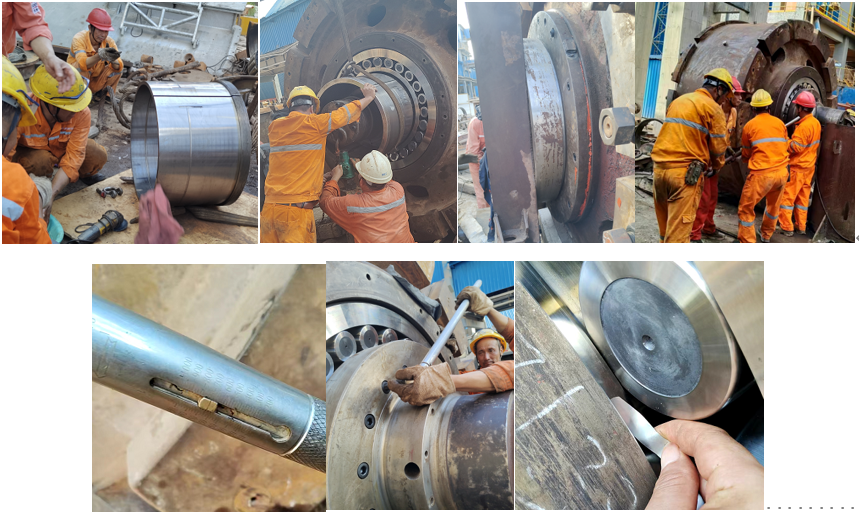
9、清理外侧端盖和隔圈、凸密封,安装外侧端盖O型圈,安装外侧端盖和隔圈。安装骨架油封。
Cleaning the outer cover, outer distance ring, convex seal, installing the outer cover O-ring, installing the outer cover and outer distance ring and then installing the rotary shaft seal.
10、清理凸密封并安装。Cleaning and installing the convex seal.
11、对中心架法兰和总成法兰进行清理,安装O型圈,吊装总成,使用液压拉伸器使用葫芦拉紧-100Bar-125Bar对称紧固M80螺栓,总成与中心架法兰接触正常。
Cleaning the center frame flange and flange assembly, installing the O-ring, lifting the assembly, and using a hydraulic stretcher and hoist to tighten the M80 bolts symmetrically at 100Bar-125Bar. The flange assembly made proper contact with the center frame flange.
三、安装过程中的不足 Shortcomings During the Installation Process
1、3#辊241/710无明显轴承型号,使用时间长,滚珠表面存在较严重缺陷,且该轴承在安装过程中发现该轴承保持架定位销断裂导致保持架移位,保持架移位导致滚珠磨损不一致,在调整游隙过程中,也发现同一位置不同滚珠的游隙存在稍许差异,因此该轴承的运行状态将会对全新的F-679545.NU安全运行产生影响,影响F-679545.NU运行状态和寿命。
The #3 roller 241/710 bearing lacks a clear model marking, had been in use for a long time, and the bearing balls showed severe defects. During the installation, the positioning pin of the cage was found to be broken, causing the cage to shift, which led to uneven wear on the bearing balls. During the clearance adjustment process, slight differences in clearance were observed among the bearing balls at the same position. Therefore, the operating condition of this bearing would affect the safe operation of the new F-679545.NU bearing, impacting its operational status and lifespan.
保持架虽然对定位销进行了更换,建议运行过程中加强对油品的检查,防止保持架再发生问题,影响轴承寿命和磨机的运行。
Although the positioning pin of the cage was replaced, it is recommended to strengthen oil inspection during operation to prevent further issues with the cage that could affect the bearing's lifespan and the mill's operation.
2、调整游隙时对压板进行人工加压的效果比使用液压螺母(专用工具)的效果差,主要表现在人工加压过程中螺栓对螺孔螺纹造成伤害,在运行中有造成紧固螺栓松动的风险。
The effect of manual pressure plate tightening during clearance adjustment was inferior to that of using a hydraulic nut (professional tool), primarily reflecting in the manual pressurization process of the bolt to damage the threads of the screw holes. This might lead to the loosening of securing bolts during operation.
3、3#轮毂内侧O 型圈位置锈蚀严重,表面凹凸,影响O型圈的密封效果,运行中有漏油的风险。
The O-ring position on the inner side of the #3 hub was severely corroded, with an uneven surface, which affects the sealing effect of the O-ring and poses a risk of oil leakage during operation.
4、其它 Other Issues
(1)二线立磨出现夹板开裂的情况,经入磨检查辊皮与轮毂的接触情况,发现辊皮与轮毂的间隙较大,最大的间隙大于0.4mm,设备安装要求小于0.15mm,因此,建议对辊皮与轮毂间的间隙重新进行调整,以降低夹块继续开裂的风险。
The second line vertical mill experienced clamp cracks. Upon inspection, it was found that the gap between the roller tires and the hub was large, with the maximum gap exceeding 0.4mm, while the equipment installation requirement should be less than 0.15mm. Therefore, it is recommended to readjust the gap between the roller cover and the hub to reduce the risk of further cracking of the clamp.
(2)三线辊皮存在辊皮与夹块的接触位置出现开裂和掉块的现状,存在运行中辊皮脱落的风险,有可能造成严重的设备事故,建议更换。
The third line roller tires cracked and fell apart at the contact points with the clamp, posing a risk of roller tires detachment during operation, which could lead to a serious equipment accident. It is recommended to replace it.
摘要:客户ATOX50原料磨利用检修时间更换磨辊轴承,我公司技术到现场对安装更换过程进行了协助、指导和监督。
Summary: The customer's ATOX50 raw mill utilized the maintenance period to replace the roller bearings. Our company's technician assisted, guided, and supervised the installation and replacement process on-site.
一、至现场时,设备的安装状况 Equipment Installation Status On Site
1、至现场时,磨辊已经解体并部分进行清洗,2#磨辊外间隔套未进行拆卸,位置确认未发生移动。
Upon arrival at the site, the roller had been disassembled and partially cleaned, with the outer distance ring of roller #2 not yet disassembled, and its position confirmed to have not shifted.
2、2#磨辊使用全新的FAG轴承。轴承型号为F-679545.NU(NU20/800-E-M1A)和F-679568.PRL(241/710-B-K30-MB-H44-SA)
Roller #2 used brand new FAG bearings. The bearing models were F-679545. NU (NU20/800-E-M1A) and F-679568. PRL (241/710-B-K30-MB-H44-SA).
3#磨辊使用一只标志仅有“GERMANY X.D”双列圆锥轴承,该轴承为已使用过的旧轴承,轴承滚珠表面镀层有明显的磨损和锈蚀的痕迹,另一只轴承型号为F-679545.NU,全新,生产商为FAG.
Roller #3 used a double-row tapered roller bearing marked only with "GERMANY X.D", which was a used bearing. The coating on the bearing balls showed noticeable wear and rust, and the other bearing model was F-679545.NU, which was new and manufactured by FAG.
二、安装服务过程 Installation Service Process
1、对部件润滑油路进行清理和检查。Cleaning and inspection of the component lubrication oil circuit.
(1)清洗前检查 Inspection before cleaning.
(2)清洗 Cleaning
(3)清洗后 After cleaning
2、主轴和轮毂清理 Cleaning of the main shaft and hub
3、内侧端盖清理、间隔圈清理、骨架油封安装、内侧空气密封内环安装。
Cleaning of the inner cover, distance ring, installation of the rotary shaft seal, the inner sealing ring.
4、用油煮NU20/800轴承内圈并安装到主轴上,安装轴承内间隔套于主轴上。过程中使用铜棒辅助安装。
Heating the inner ring of the NU20/800 bearing in oil and installing it onto the main shaft, then installing the bearing inner distance ring onto the main shaft. A copper rod was used to assist with the installation.
5、安装内侧端盖O型圈,涂抹美孚1500润滑脂于骨架油封唇口,将内侧端盖安装于主轴上并固定。
Installing the inner cover O-ring, applying Mobil 1500 lubricating grease to the lip of the rotary shaft seal, installing and securing the inner cover onto the main shaft.
6、用液氮冷冻安装3#辊外间隔套、2#3#辊NU20/800外圈和241/710轴承。检查间隔套和轴承接触正常。
Using liquid nitrogen to freeze and install the outer distance ring of roller #3, the outer rings of NU20/800 for rollers #2 and #3, and the 241/710 bearing. Ensuring the proper contact between the outer distance ring and the bearing.
7、清理安装轴承外圈和主轴,将主轴小心套入轮毂,用葫芦拉紧,促使241/710轴承内圈与内间隔套紧密接触。用支架撑起主轴,保持轮毂能盘动。
Cleaning the installation of the bearing outer ring and main shaft, carefully placing the main shaft into the hub, and using a hoist to tighten it, ensuring tight contact between the inner ring of the 241/710 bearing and the inner distance ring. Support the main shaft with a stand to keep the hub rotating.
8、清理退卸套,将退卸套安装入磨辊,安装压盘,涂抹密封胶,紧固内侧端盖,转动磨辊,现场采用人工方式逐步紧固压盘螺栓调整241/710轴承游隙,调整结果:2#辊轴承游隙为0.11mm,3#轴承游隙为0.13mm。测量轴承内圈到退卸套端面的高度为:2#平均71.24mm 、3#平均60.50mm,加工压环后,对压环按扭矩对压环螺栓进行了紧固,压环与轴承内圈接触紧密。
Cleaning the conical sleeve, installing it into the roller, installing the bearing retainer ring, applying sealant, tightening the inner cover, and rotating the roller. The bolts of the bearing retainer ring were gradually tightening manually on-site, adjusting the clearance of the 241/710 bearing. The results were that the clearance of the roller #2 bearing was 0.11mm, and the bearing #3 clearance was 0.13mm. The measured height from the bearing inner ring to the end face of the conical sleeve was an average of 71.24mm for #2 and 60.50mm for #3. After processing the bearing retainer ring, the bolts of the bearing retainer ring were tightened according to the torque, ensuring close contact between the bearing retainer ring and the bearing inner ring.
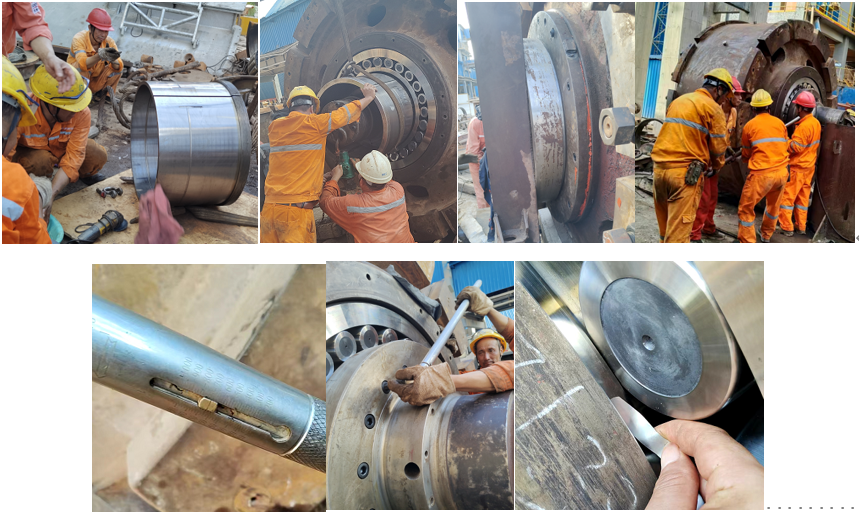
9、清理外侧端盖和隔圈、凸密封,安装外侧端盖O型圈,安装外侧端盖和隔圈。安装骨架油封。
Cleaning the outer cover, outer distance ring, convex seal, installing the outer cover O-ring, installing the outer cover and outer distance ring and then installing the rotary shaft seal.
10、清理凸密封并安装。Cleaning and installing the convex seal.
11、对中心架法兰和总成法兰进行清理,安装O型圈,吊装总成,使用液压拉伸器使用葫芦拉紧-100Bar-125Bar对称紧固M80螺栓,总成与中心架法兰接触正常。
Cleaning the center frame flange and flange assembly, installing the O-ring, lifting the assembly, and using a hydraulic stretcher and hoist to tighten the M80 bolts symmetrically at 100Bar-125Bar. The flange assembly made proper contact with the center frame flange.
三、安装过程中的不足 Shortcomings During the Installation Process
1、3#辊241/710无明显轴承型号,使用时间长,滚珠表面存在较严重缺陷,且该轴承在安装过程中发现该轴承保持架定位销断裂导致保持架移位,保持架移位导致滚珠磨损不一致,在调整游隙过程中,也发现同一位置不同滚珠的游隙存在稍许差异,因此该轴承的运行状态将会对全新的F-679545.NU安全运行产生影响,影响F-679545.NU运行状态和寿命。
The #3 roller 241/710 bearing lacks a clear model marking, had been in use for a long time, and the bearing balls showed severe defects. During the installation, the positioning pin of the cage was found to be broken, causing the cage to shift, which led to uneven wear on the bearing balls. During the clearance adjustment process, slight differences in clearance were observed among the bearing balls at the same position. Therefore, the operating condition of this bearing would affect the safe operation of the new F-679545.NU bearing, impacting its operational status and lifespan.
保持架虽然对定位销进行了更换,建议运行过程中加强对油品的检查,防止保持架再发生问题,影响轴承寿命和磨机的运行。
Although the positioning pin of the cage was replaced, it is recommended to strengthen oil inspection during operation to prevent further issues with the cage that could affect the bearing's lifespan and the mill's operation.
2、调整游隙时对压板进行人工加压的效果比使用液压螺母(专用工具)的效果差,主要表现在人工加压过程中螺栓对螺孔螺纹造成伤害,在运行中有造成紧固螺栓松动的风险。
The effect of manual pressure plate tightening during clearance adjustment was inferior to that of using a hydraulic nut (professional tool), primarily reflecting in the manual pressurization process of the bolt to damage the threads of the screw holes. This might lead to the loosening of securing bolts during operation.
3、3#轮毂内侧O 型圈位置锈蚀严重,表面凹凸,影响O型圈的密封效果,运行中有漏油的风险。
The O-ring position on the inner side of the #3 hub was severely corroded, with an uneven surface, which affects the sealing effect of the O-ring and poses a risk of oil leakage during operation.
4、其它 Other Issues
(1)二线立磨出现夹板开裂的情况,经入磨检查辊皮与轮毂的接触情况,发现辊皮与轮毂的间隙较大,最大的间隙大于0.4mm,设备安装要求小于0.15mm,因此,建议对辊皮与轮毂间的间隙重新进行调整,以降低夹块继续开裂的风险。
The second line vertical mill experienced clamp cracks. Upon inspection, it was found that the gap between the roller tires and the hub was large, with the maximum gap exceeding 0.4mm, while the equipment installation requirement should be less than 0.15mm. Therefore, it is recommended to readjust the gap between the roller cover and the hub to reduce the risk of further cracking of the clamp.
(2)三线辊皮存在辊皮与夹块的接触位置出现开裂和掉块的现状,存在运行中辊皮脱落的风险,有可能造成严重的设备事故,建议更换。
The third line roller tires cracked and fell apart at the contact points with the clamp, posing a risk of roller tires detachment during operation, which could lead to a serious equipment accident. It is recommended to replace it.