The Customized Output Ducts of ATOX50 Vertical Mill to Reduce the Abrasive Attrition and to Optimize
Publishdate:2021-07-19 Views:1048
Brief : we did a project to optimize the vertical mill of ATOX50 in a cement factory to reduce the consumption and improve the production and optimize the situation in January,2021, in China. we retrofit the spare parts and separator air system, meanwhile, we upgrade and optimize the output ducts of the cyclones to reduce the attrition and upgrade the air flow. The purpose is to low the pressure of mill system and improve the efficiency of powder selection, to achieve the requirement stable to reduce the electricity. After the preparation of the calculation, mark, engineering, data remark, and construction on site, the efficiency of air separator system enhanced as 20%, and 1.5 KWh/t low. Which are not only the cost reduced but also the competitiveness enhanced for the company.
1, Before optimization.
The dust reclaim system was applied with 4 diameter 5.6 M cyclones which existed several defects as below:
1.The cyclone out put has negative pressure till the air blower as -10.3 Kpa with the low efficiency and large attrition.
Before Optimization Control Panel.
2.The unbalanced alignment of the output air flow because of the different length of the ducts of the cyclones, which make the air blocked in the longer duct far from the blower during to the design defect that the bigger air flow can achieved near the blower, in contrary, the lower air is far from the blower. And the dust will be always blocked in the far ducts corner side as the picture showed.
blocked the air flow in the longer duct.
2,The optimized solution.
We optimized the output ducts design and replaced the unreasonable pipe to reduce the attrition of the air flow and the air hedge during to the previous design defect. Then , we combined the two pipe with one big size one to guarantee the air flow balance to the blower. We enlarge the size of pipe to the cyclones to reduce the abrasive attrition and enlarge the air flow diameter. To solve the blocked dust issue, we design and add one cone directly connected to the lower cyclone with pipe( design as picture).
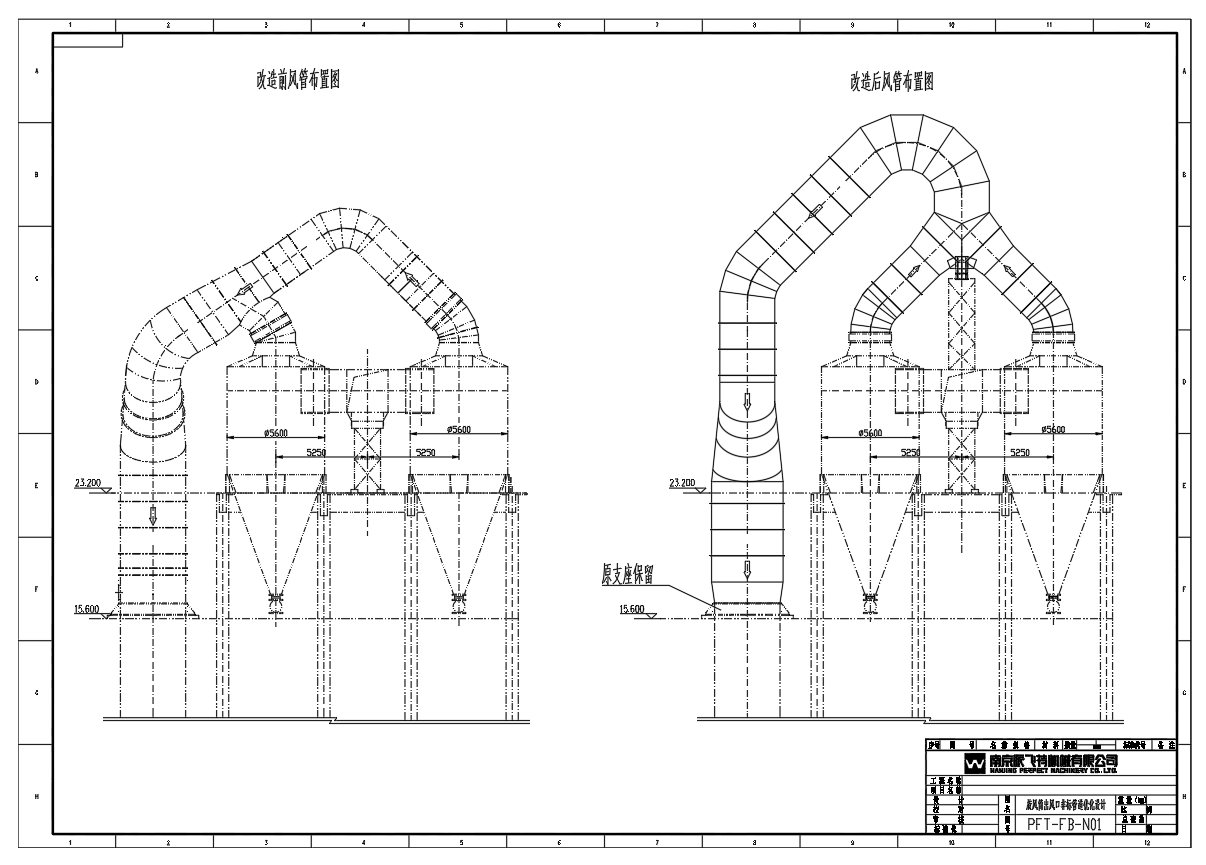
Drawing of the ducts.
3D model
3, construction
1.Remove the old ducts: cut the un- standard output pipe, keep the cyclone, and use the crane to clean the site.
2.the ducts manufacture : Connect the parts of the new designed ducts.
3.installation : Welding the pipe and prepare for the installation. At last, deal with the warm protection.
3, the efficiency of optimization.
output duct after optimization.
The differential pressure are reduced after the design optimized, and the output pressure declined as 1500-2000Pa and the efficiency of air separator improved.
Brief : we did a project to optimize the vertical mill of ATOX50 in a cement factory to reduce the consumption and improve the production and optimize the situation in January,2021, in China. we retrofit the spare parts and separator air system, meanwhile, we upgrade and optimize the output ducts of the cyclones to reduce the attrition and upgrade the air flow. The purpose is to low the pressure of mill system and improve the efficiency of powder selection, to achieve the requirement stable to reduce the electricity. After the preparation of the calculation, mark, engineering, data remark, and construction on site, the efficiency of air separator system enhanced as 20%, and 1.5 KWh/t low. Which are not only the cost reduced but also the competitiveness enhanced for the company.
1, Before optimization.
The dust reclaim system was applied with 4 diameter 5.6 M cyclones which existed several defects as below:
1.The cyclone out put has negative pressure till the air blower as -10.3 Kpa with the low efficiency and large attrition.
Before Optimization Control Panel.
2.The unbalanced alignment of the output air flow because of the different length of the ducts of the cyclones, which make the air blocked in the longer duct far from the blower during to the design defect that the bigger air flow can achieved near the blower, in contrary, the lower air is far from the blower. And the dust will be always blocked in the far ducts corner side as the picture showed.
blocked the air flow in the longer duct.
2,The optimized solution.
We optimized the output ducts design and replaced the unreasonable pipe to reduce the attrition of the air flow and the air hedge during to the previous design defect. Then , we combined the two pipe with one big size one to guarantee the air flow balance to the blower. We enlarge the size of pipe to the cyclones to reduce the abrasive attrition and enlarge the air flow diameter. To solve the blocked dust issue, we design and add one cone directly connected to the lower cyclone with pipe( design as picture).
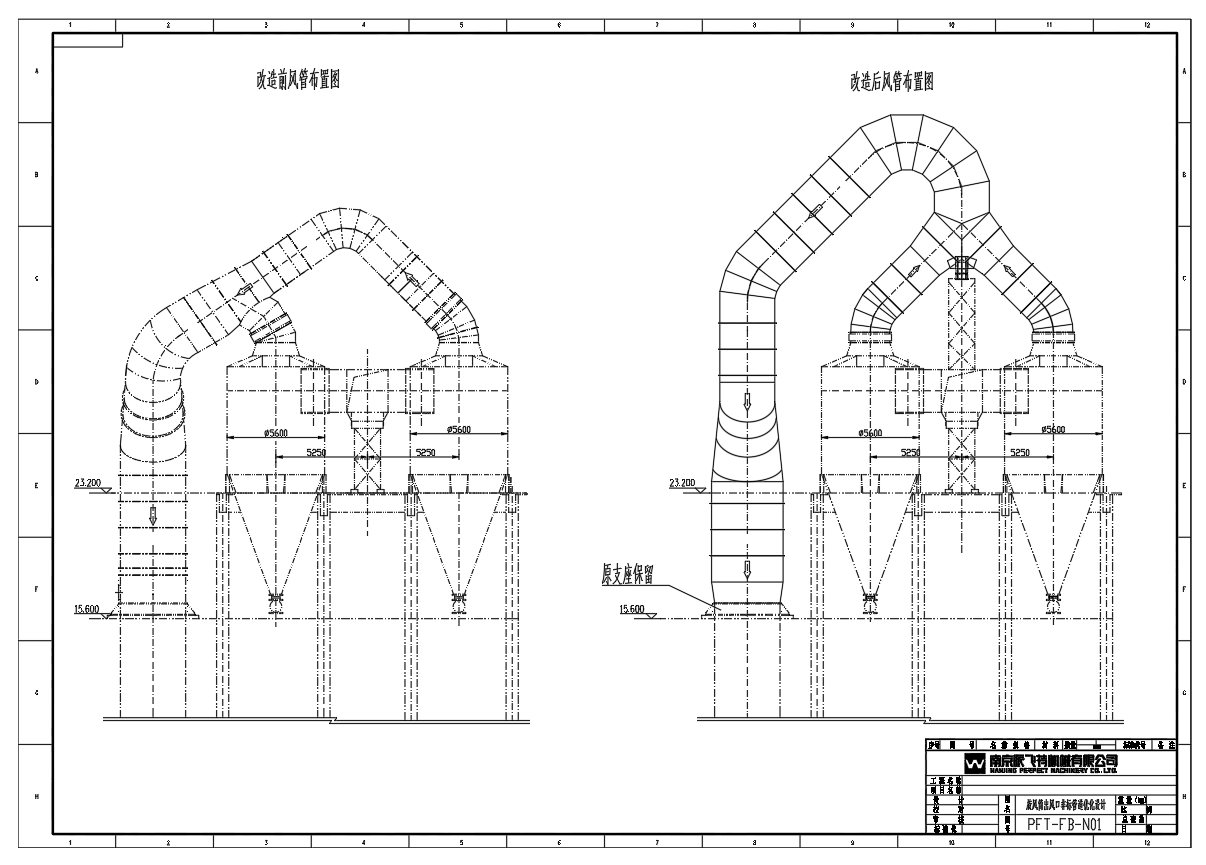
Drawing of the ducts.
3D model
3, construction
1.Remove the old ducts: cut the un- standard output pipe, keep the cyclone, and use the crane to clean the site.
2.the ducts manufacture : Connect the parts of the new designed ducts.
3.installation : Welding the pipe and prepare for the installation. At last, deal with the warm protection.
3, the efficiency of optimization.
output duct after optimization.
The differential pressure are reduced after the design optimized, and the output pressure declined as 1500-2000Pa and the efficiency of air separator improved.